Surface System
Automated Surface Equipment
Erdos Miller values automation at the rig site due to its direct ability to improve safety. Automated rig equipment can operate 24 hours a day without fatigue. We believe that by simply monitoring equipment at the rig site will provide a benefit of reduced down-time through preventative maintenance programs.
We have all heard about IoT and Artificial Intelligence. These are buzzwords that you would be hard pressed to avoid. In the upstream oil & gas industry it is no different. In particular, the drilling site itself has a mixed bag of legacy equipment with no sensors, and some pieces with isolated sensors only providing limited value to its manufacturer. For those manufacturers able to collect data from their equipment even fewer are using that data to make decisions.
As engineering consultants for upstream oil & gas we believe we bring a unique perspective and moreover experience to help companies that are interested in getting a return on their investment into smarter equipment. Just collecting the data is not enough, you must also know how to store that data so that it can be interpreted. Through machine and engineering interpretation, manufacturers will then be able to unlock the benefit of adding sensors to its equipment by incorporating preventative maintenance for existing product lines, and improvements for future product lines.
Our Experience
We draw upon lessons learned in other industries that have already gone through this IoT and smart sensing revolution. A few of these lessons should be straight forward but in many cases are overlooked. The first of these is actually the most overlooked. The user interface for the device is one of the most critical aspects of the device. Even if you spend thousands of hours designing a near-perfect data acquisition system for your equipment, if your field personnel cannot make quick decisions based on the information presented, then it will all be a waste. Your user interface must be able to take in all the data, make some behind-the-scenes decisions and present only the most critical information to the user. The field users work long shifts, and must be able to identify issues immediately and be able to act quickly. Moreover, the engineering team should be able to jump under the hood and debug issues without cluttering the view of the field personnel. Thus the user-interface ends up being a balancing act between practical and technical which Erdos Miller has successfully deployed on many equipment types.
The second lesson we have learned is that there is a balance between computing power at the device and in the cloud. On one hand, cloud computing is likely the best place to process vast sets of data. Many machine learning companies will deploy their solutions in the cloud to leverage the computing power and data storage capabilities. However, the clear drawback in this scenario for a drilling equipment manufacturer is that you will need to get all your datapoints into the cloud. The areas where the oil & gas industry are not normally blessed with great internet! Most internet is provided through a cell card or satellite connection and sending all data to the cloud will quickly run up a serious tab with your connectivity provider. The lesson we have learned is to perform some of the processing and decisions at the device before packaging to be sent to the cloud. Some techniques would be to average data when reasonable. An easy example is when you can sample pressure data 1000 times per second and no pressure changes occurred during that time, you can send just a single packet instead of 1000. Another easy example is when sampling temperature, you likely don’t need 1000Hz data, so sending this value once a second or even minute is usually sufficient depending on the equipment type.
Each equipment type brings new challenges and lessons learned. We aren’t an expert in all drilling equipment but I can bet we can save you some lessons learned if we embark on a project together for your specific equipment. A short-list of some equipment types we have direct experience with are:
- Centrifuges
- Top Drives
- Mud Pumps
- Frac Pumps
- Torque Tools (Iron Roughnecks)
- Blowout Preventers (BOP)
- MWD Surface Gear
- EDR Systems
For those savvy enough to embark alone
Some companies will have enough experience to embark on IoT/smart sensing projects alone. That does not mean you have to solve all of the problems that have been solved by the companies that came before them. We have a few free tools that we offer to those brave engineers who wish to develop projects internally. We use these tools when releasing product lines, so why not help others so that we can all start solving some bigger problems together? Let us introduce a few tools to help keep you from re-inventing the wheel and allow you to focus on solving some big problems.
So, you're collecting data already?
As some board member in a suit likely has already told you:
The project is straightforward:
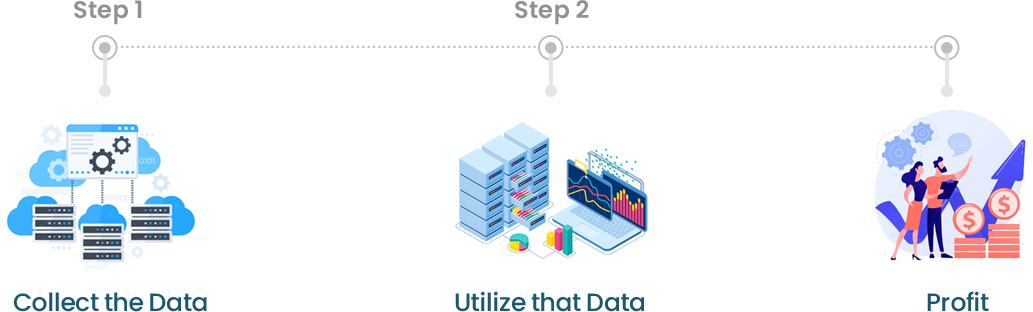
You may have thought to yourself already, “Okay, but what do you mean by 'utilize' ”. We had the same experience our first time adding sensors to equipment. Very quickly in fact, we found that the data gets overwhelming in a hurry. Imagine trying to interpret or graph millions of points in Excel. We developed a tool internally based on LabVIEW which helps to correlate different data sets all in one place. WAVE is our data visualization and interpretation software that we offer fellow engineers and data analysts, for free! If you would like to learn more, Click here to learn more.
Need to Interface with other systems at the Rig Site?
We can help transmit that data to other systems on the rig site. In North America, the standard protocol used is called Wellsite Information Transfer Specification or WITS. This protocol allows Operators and Service Companies to develop systems and have a standard means of communication between them. For the curious developer we have a blog post that goes into more detail Here. For the rest of us, WITS is important because if your equipment is expected to provide data to the EDR you must use this protocol.
In addition to communicating to the EDR, some systems rely on data from others to make decisions. An example of systems that require one another are MWD surface systems. They provide drilling information collected down-hole to the EDR and enable the directional driller to make decisions in real-time. One of the improvements that is known to make a MWD surface system better is to know the actual depth. In most systems this relies on a user to input the depth information, but some systems have an input from a hookload sensor or even a WITS port to receive that information for a more reliable input of well depth to the MWD. Imagine if the mud pump could send sensor feedback to the centrifuge when there are too many solids hitting the pump. This isn’t rocket science, it is a very realistic scenario thanks to WITS.
If you are developing the software interface to speak WITS and would prefer to test in the lab rather than at a rig site, then you are in luck. We developed a software application called the WITS Simulator to do just that. As fun as live rig tests are, we like to validate as much as possible before going live so that we do not impact the rig performance and potentially introduce non-productive time (NPT). The WITS Simulator will allow you to generate and receive WITS traffic to test your application in a low-pressure air-conditioned environment. For more information about this free tool, Click Here.
Our Limitation
If you’ve read this far you might think we’re experts. Although we have experience and have learned plenty of lessons, we have plenty of lessons yet to learn. One area where we do not have expertise is in data science. Although we’re not data scientists, we have been the interface between the manufacturer and machine learning company. We prefer to stick to upstream projects and let the machine learning/artificial intelligence companies do what they do best. This allows us to focus on collecting the data, and packaging it to be handed off correctly and consistently.
Downloads
WAVE-Data analysis software- Erdos Miller
A data analysis software package that is focused on analyzing both real-time and recorded memory for drilling devices on a graphical workbench.
WITS Simulator
Get this simple tool for developing and testing WITS-based communication devices and software.
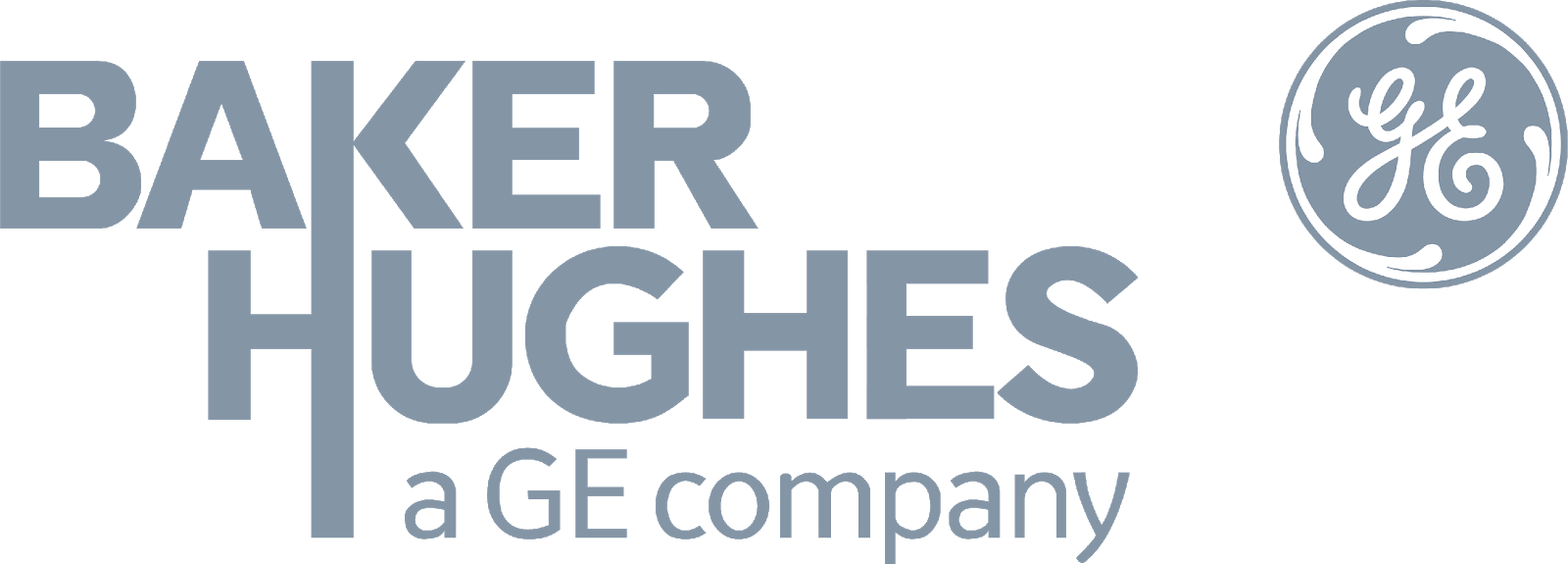



