The Relationship Between Testing and Product design
Season 2
This episode is sponsored by
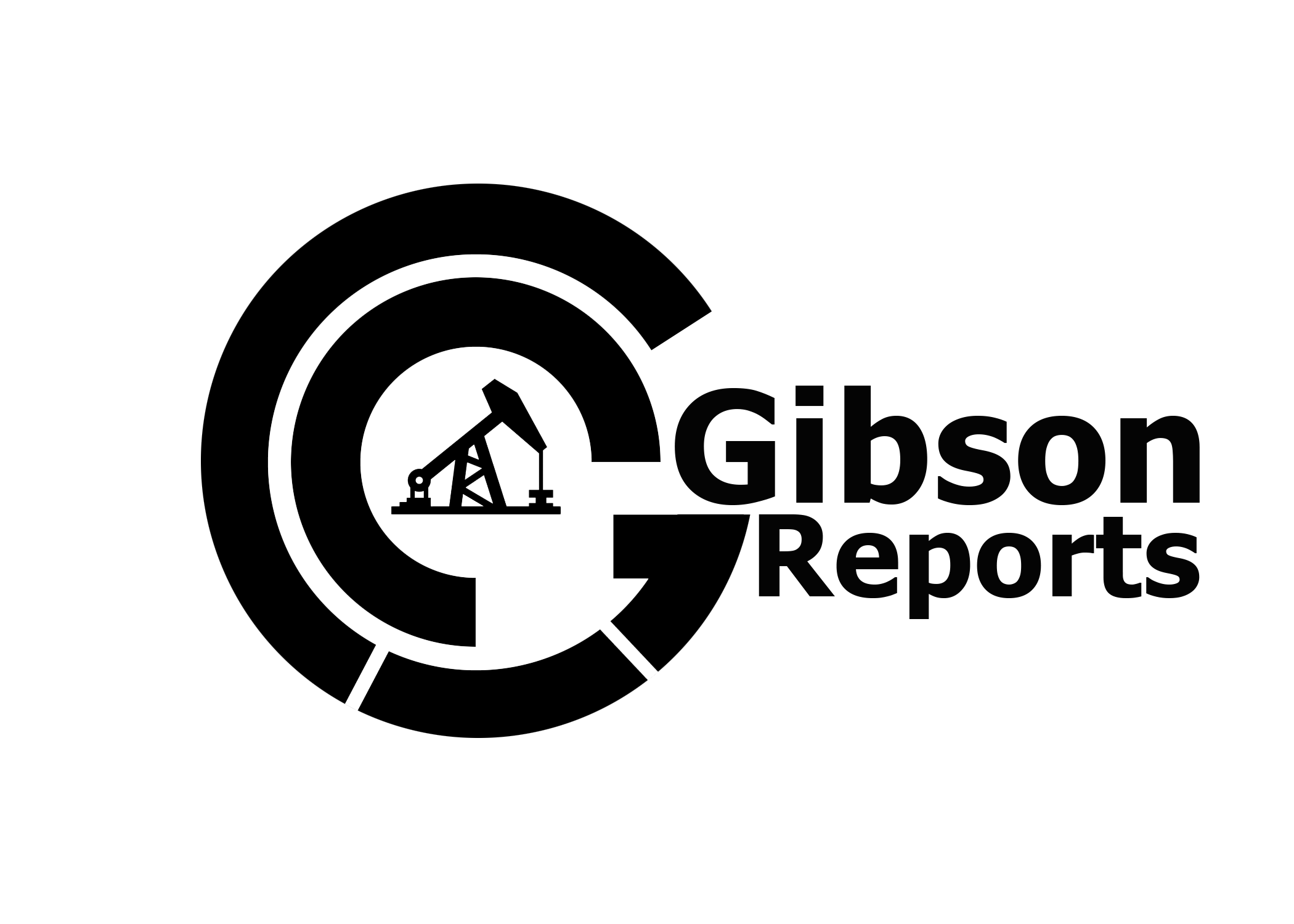
David and Ken welcome guests Bob Joyce and Eric Allen from DynaQual. Topics discussed include simulation of the downhole environment, HALT/HASS, and is thermal cycling even worth it? Press play to listen in on our take on these topics.
***Thank you to our Sponsor Gibson Reports!***
Welcome to the Erdos Miller New Technology podcast, where we spend our non-productive time talking about everything drilling tech. I'm Ken Miller.
And I'm David Erdos.
Today we'll be talking about electromechanical product testing in the extreme downhole environments, which is way more exciting than it sounds. Yeah, so our podcast season two is sponsored by Gibson Reports. They produce excellent integrity and directional drilling market share reports. Check them out on gibsonreports.com. And remember, you can check us out on Spotify and iTunes, just search for Erdos Miller.
So today's episode, we'll be interviewing Bob Joyce and Eric Allen from [inaudible 00:00:32] Why don't you guys start by giving us some brief introduction kind of to your background, [inaudible 00:00:36] and kind of specifically more on the testing side of things?
Sure. My name is Bob Joyce and I'm the founder and President of DynaQual Test Labs. I've been in the product development area for many of my career days, looking at a product development similar to this that you do here.
Mm-hmm (affirmative).
And in product development, there's just a lot of need for getting quality systems built, tested.
Especially in this industry.
Absolutely. In our own industry, it's very important. And I just got a keen interest in that area, in the different projects I've been involved in, and decided to do it on my own and help others that don't have the means to do so. So it's something that's dear to my heart.
Okay, great.
Yeah, I'm Eric Allen. I'm a Business Development Manager over at DynaQual, but as you'll find with us, everyone wears a different hat and that's a testing hat. So everyone's involved in our testing there at DynaQual. Previously, I've worked in MWD...
Oh really?
Yeah, doing technical work even on the holster units and batteries and those kinds of things.
Cool. Which one was that with?
With Ryan up in Canada.
Ryan. Okay, pretty good.
Mm-hmm (affirmative) Like in '07.
So what inspired you to start DynaQual?
Great question. Getting back to what I just mentioned, the companies and projects I worked on, I asked the teams to look at project plans and test plans. And it wasn't easy to do in this area. And a light bulb came on and then said, "I'm going to put a business plan together." So seven years ago, we kicked off DynaQual to provide to independents and also to the majors, a suite of testing services for working with [inaudible 00:02:35] all inputs.
So we started obviously in the oil and gas industry where I started, and we diversified into the market segments that the oil and gas area in the downhole segment is the biggest one.
Yeah, I think it's really [inaudible 00:02:52] since you guys have been around, a whole new set of tests and machines have become available to people that otherwise wouldn't have had the means to pick up the machines. Because investing in a lot of that stuff and getting it going yourself at a small company is pretty taxing, right?
Absolutely. That was the basis of the business case and it's worked out quite well.
So talking about the design and development of all these different types of electromechanical devices, which has been mostly my background. Mostly the thing I've been involved with has... it's got a circuit board somewhere, right? It's not just purely a piece of metal or a few joints or something.
So what are the different types of testing that you guys would usually recommend or offer for devices like that? Because it's not just one test, there's lots of different types of testing. Can you guys kind of go to the basic categories of testing?
Yeah sure. In the testing area for downhole products, the suite of services that can be offered is anywhere from thermal to vibration, to pressure. And then of course, there is the more in situ testing that you can do that we can talk about in a minute, like in flow loops and things like that. So combining these, is a very good asset to the testing practices.
Okay.
Like combining thermal and vibration.
Mm-hmm (affirmative).
And so new products have come out in the last decade or so to aid in that process, that's where you come up with a HALT and half processes.
Mm-hmm (affirmative).
And then when you combine thermal and vibration, that has its benefits. So you combine those together, it gives you, provides you a good suite of testing services to help simulate downhole conditions.
And those might be in the oil and gas industry. All these stresses arise naturally from the drilling process, right? So we're putting these tools underground and the deeper you go, the hotter it gets in general. And so, what's crazy to me is that we end up in this industry, building electronic devices that you wouldn't do this for obviously agentic reasons, but you could put some of these devices index to an apple pie while it's baking, and be just fine, right? That's how extreme some of these temperatures are, right?
Right.
You put [inaudible 00:05:08] You put an iPhone in there. It's going to be a really nasty, toxic mess. And these devices, they go in and come out and they're meant to be just fine. And so we have the high temperature from being underground, and then also the drilling process. So we're down there, we've got a drill bit and pipe and we're pushing on it and breaking up rock, and all that kind of stuff. And that causes all sorts of crazy vibration.
So I would ask, so the test machines that are typically used in the industry for vibration are designed to kind of simulate those shocks and vibrations from the drilling measurements, or from the drilling operations, right?
Absolutely. Even today, the apparatus doesn't provide all of the exact downhole conditions in the way they are. And that's why you look at a combination of tests.
Mm-hmm (affirmative).
Like for instance, with vibration, you get the low frequency content of the vibration test, but it's only unit directional. Most electronic [crosstalk 00:06:07].
When you say unit directional, can you just expand on what that means?
Okay. So looking at all of the three axes in the drill string for instance,
Because we're in three-dimensional space.
Three dimensional space.
Okay.
Yeah. The axial direction, and then you have the axial directions and the longitudinal directions, right?
Mm-hmm (affirmative).
And those are the three. And then you have [inaudible 00:06:27] pitch and role, which gives you the torque axes.
Okay.
And that's where HALT practices come in, where the vibe simulates that more. However, a HALT chamber does not get all of the move frequency content [crosstalk 00:06:42] or in the shock.
So what we ended up having is this kind of battery of tests that we can do in the industry, which is suggesting devices, the high temperature, or even high humidity, right?
We have vibratory testing where we're putting different frequencies of vibration, shock testing as well. And those would all be kind of individual phenomenon tests, right? And then we even have the ability to kind of multiple at the same time, you can do vibration and temperature together, which is even one step closer to be more realistic.
Absolutely.
Okay.
Tell us about a project where testing really made a big difference to the liability of the product?
Sure thing. I'd like to answer that in a general sense.
Right.
What really, I guess pleases me is when an engineering team comes in to do a test, whether it is vibration or HALT or HASS even. And especially in the engineering phase development, they come in with a very confident being about them. And at the end of the test, they go, "Wow. Was I glad I did that because I see three areas where I can make an improvement."
So you haven't seen too many places that come in and do the tests, and it's like, "We were fighting the first place, but you can really get [crosstalk 00:07:51]"
You can get a few of those.
A few of those, okay.
But most tests, we [crosstalk 00:07:56] That's right, and we learned something too.
So is this a roundabout way of saying every project that you include tests on, goes better?
Absolutely. Every repeat tests that there're improvements, and our customers also have found budget and time to make those improvements and return to do the test. And then they see what we call the check mark and then they leave. And they're mean time between failures, downhole increases dramatically. And we've had a number of those success stories come through.
Because the testing reveals so much about your design. And that's what we see that is a crucial of every test, is when they put it on the table and they see something on the design level, they're like, "Oh, we need to go back and change this board. I know you guys previously talked about it. And we find a little piece that's come off in vibration and they're like, "Oh, great. That wasn't on there, right? Let's go back to the drawing board and do it a different way." And then come back and do the test again. And like Bob said, we see that success. That's what we like to see at DynaQual.
My answer to that question is one of the best projects I've ever been on is we kind of went into it with sort of an unlimited test budget, which kind of seems a little insane. But what we did is we really focused on the whole testing, which was the combined vibrant... Sorry, vibration and temperature. And we just took the device we were designing and we just kind of had the mentality that we're going to break this thing until it doesn't break anymore.
And I think we ended up going through over five rounds of HALT testing, it was a lot. It was five revisions of the board, five HALT tests, and we just kept pushing the limits and breaking it. And we were prepared to continue doing that until we had the best project imaginable. And that was just a really interesting experience in my career. And it was a huge benefit to the client we're working on it with. And we ended up with one of the designs that I'm the most proud of.
And I think being kind of unstoppable and unrelenting, it was a key factor, as well as being able to have that test apparatus and just keep breaking those boards. And so, we've absolutely seen that and testing is just such a huge part of what we do here. And so it can really make the difference in the overall quality. You can end up with a... It's funny, it takes a lot more to go from like a B product to an A+ product when you think, but it's absolutely worth it in the end.
Absolutely.
So what do you think the biggest thing that's changed in our ability to test for these kinds of downhole devices in the last 20 years?
Well, we have touched on it, but I think one of the biggest additions to the testing area is the HALT HASS process.
I'm going to have to stop you and ask you to tell us what HALT and HASS means, because those are not words in English, right? [crosstalk 00:10:42] They're acronyms, right?
Make assumptions, right? Yes. HALT is Highly Accelerated Life Testing.
Okay.
So it's actually a destruct test, where it focuses on the processes during the engineering design phase primarily. You can go back with a production article and HALT it of course, to make improvements. But if you're in a new design, it's really great to start with the HALT process, for the reasons we've been talking about. And through the process over matter and highly accelerated, meaning two to three days, not over many, many days.
Yeah.
We would apply stresses to the articles and work them till they show loss, and then try to back up from that and keep them in an operating state to learn what improvements can be made throughout that process.
I'm going to interject a little bit of trivia here.
Sure.
So I actually learned this recently. HALT is an acronym because you pronounce it, right?
That's correct.
So things like FBI and CIA are initialisms because you don't pronounce them. So you'd be wrong to say that FBI is an acronym.
Uh-huh (affirmative).
So I tho that was kind of interesting. It's fun trivia I didn't know.
That is right.
What's interesting about HALT is if I'm trying to make a certain [inaudible 00:12:10] last at 175C, HALT has no recommendation as to what temperature that device needs to be tested at. It's a [crosstalk 00:12:17] process of discovery of the limits of the device, which makes it such an interesting process.
Absolutely.
And then on top of what you're saying, there is no... Your goal isn't really to come out and say, "Oh yeah, we've got four paths." Really, your goal is to come out and say, "Okay, we killed all of them, and here's what we learned about doing that. And here's where we learned our weak points for." And then you have to decide, "Okay, is this weak point... Is this good enough for my specification? Is this weak point very unlikely to happen in the field or is this pretty likely to happen in the field? And I really need to rep my design to get rid of that," right? [Crosstalk 00:12:50]
In my personal experience, what's been most interesting about HALT is before, when we just had the ESS or Electronic Stress Screening or Environmental Stress Screening, sorry. Which is basically just a fancy word for temperature, high temperature. What we could do prior to HALT was we could find two things. We could find through ESS infancy failures of our high temperature electronics. So if we had a new design and it only lasted 50 hours, well, that was pretty easy to figure out with an oven, because you could just make it up the circuit board, put in the oven. Okay, it's filling me 50 hours, find the problem, rev the circuit board, do it again.
And then we could also find kind of our long term thermal limits, because once you get past the infancy stuff, you're really not going to have much more problems again with just high temperature, until you get into a lifetime in the silicon. And so you might have something that's in the oven for a 1,000 hours or 2,000 hours. And I say silicon because most of these devices these days have a microprocessor, or at least Gates and MOSFETs and all sorts of stuff on them that have thermal limits.
And so, there really wasn't too much middle ground stuff that we found in ESS. It was all either right at the beginning or it all ended up being kind of like this long lifetime stuff. And all the middle ground, failures used to be really painful though to find, because all we have to do is build the devices, send them out to the field and then kind of see where they start failing. And that was usually involving a lot of customer pain. And so, it was always interesting to me about using the whole [inaudible 00:14:17] process, the whole machines and the whole testing methodologies.
I feel like it really filled that middle gap and gave you a good way to precipitate failures that would otherwise have only have occurred once you'd made production devices and give them to customers and running them downhole. And so I feel like today out of the gate, if we do a full battery of shock testing, ESS, HALT testing, vibration testing, you really pretty don't likely when you go to the fields the first time, to have a successful run. Really, there's a lot that we can do these days to really get these devices ready ahead of any time a customer puts some hands on it, right?
Absolutely.
So HALT testing was the biggest thing you think will last 20 years.
That's one of the... Once this pans out of course.
Okay.
Yeah. And then on the HASS side, if I may touch on that, that is Highly Accelerated Stress Screening.
Right, and the highly accelerated part just means taking the schedule from months and months of field testing, and compressing it down to something that's attainable in the lab, in a designed amount of time, right?
That's right. Half a day for many of them, on the standard HALT converted to a HASS.
Yeah.
And whether you take the limits that you determined in a HALT, and reduce them so that you do not take the life out of your product. You don't want to do that, you want to take just minimal amounts of time of your commercial product, and you put them in the chamber and do a much less aggressive test in just a few cycles for [crosstalk 00:15:49]
So what you're saying is HALT is pretty securely for the design phase of things.
That's right, yeah.
And then HASS is also... That's probably the manufacturing side of things, right? [crosstalk 00:15:59] So what you're saying is what is possible today is that we can define a screen, because every time I put stress on these units, I'm taking a little bit of life out of them, right?
That's right.
But it's possible to set up and design a screen, such that we can take a little bit of life off the units, enough to prove that the quality's there without significantly impacting the life from our clients would see in the field. And it wouldn't feel like they paid for a 100% of the product's lifetime, when they got 80 or something, right?
That's right. A properly executed HASS, you want to try, if there is a production law, latent defect, then you want to make sure that you can get products that going out of the door, they're less than 5% drop out.
Okay.
Obviously 1% to 2% is ideal.
Mm-hmm (affirmative).
And the other side of the point, if you do a whole year's worth of lots in a half and you see nothing, then you may want to redesign your HALT even, and/or your limits in your HASS to stretch them a little bit more, to look at your limits and see what they can take.
And so ideally I'd put every device and manufacturer to this HALT screen, right? What happens when I'm making 10,000 a month? Is that realistic?
Not always.
Okay.
Not always. Again, depends on the critical nature of your task. Many people will also just take samples but always do one if you change your processes, or you change your vendors, or the lots are very different.
The reality that we're almost faced with a lot in these electromechanical device manufacturing is that the sustaining of the portion of the device's life cycle is so fluid now, that you're almost constantly having to change. A lot of the semiconductor manufacturers, a lot of the different even resistor capacitor manufacturers, board manufacturers, it's really improbable these days that you could design a device, specify all the components and all the manufacturers, and then have no changes for 10 years, and just keep making the same thing.
There're all sorts of issues that affects supply chain and the components that you can get in there. You might have some sort of European capacitor manufacturer, and all of a sudden they've got tariffs. S now they can't supply capacitors fast enough for the capacitors. Or somebody goes out of business and they can't supply a part, or they discontinue a product and they don't have five years of lifecycle.
Right. So I would say the vast majority of products that are in sustain right now, really need to be looking at this process, is because I'm really skeptical that they're just manufacturing in the same old way they have been for the last 10 years, unless they're just doing a few of them really slowly. So if you've got anything that's modern, high volume, you're in there and you understand that your supply chain, your sustaining product is a living, breathing thing that's changing all the time. Right?
Right.
That's right.
So we're obviously talking a lot about testing down the designs, but how close do you think HALT and HASS really get to stimulate in the downhill downhole environment?
Well, that goes back to our comments about the HALT and HASS system does not really even care where the product is going.
Right.
We kind of touched on it.
Yeah.
And that's what the issue that I have with many customers that come in that don't understand it totally. They go, well, "I'm not going to minus 40 with my product." I said, "I don't care. I'm looking for engineering design weaknesses."
Yeah.
[crosstalk 00:19:37] because we're working downhole so much that high temperature is obvious the right thing to do in cold temperatures like, "What? Why are you wasting my time? I'm not drilling in Siberia." I just said the biggest thing for us as electronics guys is that the high temperature stresses the silicon. It stresses the electronics for the board and how they're operating.
The low temperature stresses mechanically, how the board comes together. The solder joints and the placements and all this kind of stuff.
That's great.
And the layers on the board. And so that's what I really value about going to cold temperature.
Correct.
But to elaborate on your point, could you use HALT testing for similar products or aerospace, all that kind of stuff, or were these machines built specifically for oil and gas?
Oh no. They're made for all products that need robustness built into the product and reliability improvements.
It doesn't even have to be extreme environments.
No.
I could use this to design a better laptop.
That's correct.
You're not going to put 85Gs of random vibration on a laptop, right? But you might put five, which would be a lot for a laptop, right?
That's right.
Okay.
So the limit may be 25Gs on a laptop before it starts to show saw failures.
Mm-hmm (affirmative).
And that's when you stop the process. So you don't go to the limits of the machinery, and all products have different limits, but the end result is still the same.
Okay. So would you say we're pretty close to something in the downhole environment, or kind of halfway there, or a lot to be improved?
You mean with just HALT and HASS or all testing?
With all the testing we have today.
Individually, they all have their strengths and weaknesses. And so, the answer is not totally, but one pie in the sky ideas would be as if many of these inputs can all be applied simultaneously. And the only way to do that right now is to go to a drilling environment.
Test rate or something, right?
Test rating [inaudible 00:21:37] out in Colorado. Or you have your own like many other majors have, but it's very expensive.
Now, the only bit of feedback I have on that is... And we've done all the testing in facilities like that, and they're very valuable, right?
Yeah.
But even that is not all the way there, and the reason there's still a gap there, which sounds crazy to say, that you're going to go ahead and just hire a rig and do the downhole drilling. Often, the remaining gap is that the drilling rigs of those facilities might be a little dated. And often the guys in the field have the latest, biggest rigs, the biggest palms, the noisiest, most powerful top drives, and all this kind of stuff.
And so, in the latest downhole tools, using them in the latest, most aggressive way...
And they're shallow.
And they're shallow, right? And so, I guess all the lab testing; HALT, HASS, ESS [inaudible 00:22:32] I don't know what I want to say, what? 75% of the way there. And then the test rig might get you 85% of the way there.
Correct.
We're 90% of the way there. I mean '95, but there's still a gap. You're still not quite there even when you go and hire a test rig.
Definitely a point of diminishing returns on that.
Yeah, there is.
That's why most people don't do it.
But that's why you still get surprised when you go to the field sometimes for the first time. If we had a theoretical test machine, they could perfectly [inaudible 00:23:03] the downhole environment. Then we should be able to completely in the design phase of a project, have a product that's ready to go, that you can manufacture a 1,000 of, and have close to zero issues. That just never ends up being the case, right? So
Ironically too Ken, many issues related to downhole technologies is the complete system checkout when you go to the field.
Yeah, true. [crosstalk 00:23:25]
So many little items that can come into the equation, that can eat your lunch, so to speak.
Yeah.
But the more and more tests that you can do, subset, if I may use that term. Obviously helps in the total process.
And what you're saying, right now we're able to test a bunch of these different drilling sub assemblies, but often, the overall device that needs to do the job is coming together at multiple of those sub-assemblies. And that's one thing that kind of alludes us still today, and the testing is that often these things are just too... Especially in drilling when these things are often 30 feet or 60 or 90 feet long, when they get all put together, it just ends up being a system that's never been, "Tested," as a full system because, we tested the sub-assemblies, but those systems are just too big built together that when you put it down holes, it's sometimes being tested for the first time. [crosstalk 00:24:13].
Okay, that's crazy. So a big question we have from our customers and I've seen the industry being pretty divided on this. So you're in the drilling industry, this affects the directional drilling guys a lot because they're obviously very used to having electronics as part of their business, but this is going to impact more and more people as how you get more things like electronic data recording systems, and smart motors and [inaudible 00:24:36] systems, all this kind of stuff.
The customers like to ask about... We have obviously the manufacturing time of the product before it's sold or given to a customer, and then whatever screening that happens there. And we're big advocates of doing lots of screening there. But then the customer has a question, "Okay, I've been delivered a device. I own that device. I expect to own that device for a certain amount of lifetime. Do I do my own additional screening during the lifetime of that device?" And what that usually boils down to, especially if the directional drilling guys is, "Should I be running thermal cycles on my modules?"
And so a lot of them these days, like I said, it's pretty divided. Half of them will say, "Yeah, I'm comfortable doing that," and I feel like that gives me some extra quality assurance before I go to the field, doing these thermal cycles before things were being run. And then someone will say, "Okay. Well, I know that every time I do that, I take some amount of lifetime off the device. I really don't want to be doing that. I paid for this device, I probably paid 20 or 30 or a $100,000 for it. Every minute it adds up to some amount of dollars. Am I taking off too much life when I do that?" And so I'd love to hear your opinion on that for the industry?
Sure. That's a great question. The benefit we have in our environment is we get to see and hear what the collective does in their own environment, including the majors. And many customers I can say, will do screens in between any maintenance schedule and/or a time schedule. And so, my opinion is that I think it's good to have a controlled screening process, but I don't actually don't feel that it should be just thermal.
Okay.
I think thermal and vibe is very important. And many of the suppliers out there do put their tools, whether they're new or used, through an ESS process before they go to the field.
Yeah.
Environmental Stress Screening [crosstalk 00:26:40]
I think that's kind of a sense of the equipment available, It's pretty affordable to get like an oven for this kind of stuff, but [crosstalk 00:26:48].
Then when you have the vibe portion...
Yeah, cost goes way up, right? It's like a $5,000 device going to almost a quarter million dollar device.
That's correct.
So you're actually saying what you would recommend that would be ideal is even during the product's life cycle, if it's expected to have a $2,000 life cycle, maybe every 500 hours, you do a temperature and vibration screen.
That's [inaudible 00:27:11].
And I guess the idea there would be just be to... If there's anything else that might be on the verge of failing, as opposed to it failing on the next run, kind of trying to precipitate that in the controlled environment and addressing it there, as opposed to addressing it with a failed tool, with a run for a customer, right?
Absolutely.
And even in my background, when the tool would come back and there was troubleshooting required, they might put some thermal blankets on it and put it on a little vibe table.
Yeah, yeah.
And hit it with a hammer. And they're like, "Oh, pulsar is moving, let's throw it back in the field." But it would come back and there'd be another failure on it. So in troubleshooting, that's where we're talking about, we need to make sure that there're these kinds of screens in place so that the people, the customer that's paid all this money for the equipment, aren't just thinking, "No, this is good enough and they can send it back in the field." You have a certain standard that you know, "Okay, I can trust that this hasn't decreased a lot of the reliability of the tool. It's gone through a troubleshooting process. And now I'm confident that I can send that back to the customer, not have a downhole failure."
The good thing about adding the vibe is it helps precipitate that failure, a little quicker than just doing thermal.
Okay.
If you have an electromechanical issue.
Right.
Solder joint.
And that totally happens.
Cracked board, whatever.
I'm not going to pretend like stuff that I design never fails, I wish that was the case. But often it'll be... We've had issues where, okay, the device we're operating is fine, operating is just finding thermal, and then you put size amount of vibration on a downhole, and there's a solder joint issue, and it's been cracked. So that almost kind of proves your point right then and there.
That's right.
It doesn't matter if it's... When you have a launch from mechanical assembly, one solder joint might be the difference between a failed run or not.
Mm-hmm (affirmative).
So there we go.
And then they can be intermittent. [crosstalk 00:29:04].
So going back to the design phase, when you design a product, how do you know if you're testing too much, too little, or what's the right balance there?
When you're testing in the design phase, again, I'm going to point to where you carefully go to failure modes, but failure modes first. So the big word is you don't want to induce a failure.
Just to clarify a little bit, you mentioned soft failures. Can you maybe just clarify what [crosstalk 00:29:42]?
A failure where the article will not operate the way it should, or start drifting and as you're monitoring it of course, in the electronics. And if you backed off on the stresses, whether it be vibe, thermal or both, you see it come back to life. So that is an essence of soft failure.
So it is the opposite of firm failure?
Hard failure.
Hard failure.
Hard failure of course, is one where you can't bring it back, and that's what you'd try not to do. And so, that's what I was getting to the answer your question.
So to give more character examples. So if I have a circuit board name and I have a component on there. So it's a soft failure even under vibration, maybe that solder joint's kind of cracking a little bit. The device becomes kind of intermittent, but as soon as I back it off, it goes back to working [crosstalk 00:30:30] making contact again. Example, the hard failure would be that little component, flies off the board. [crosstalk 00:30:35]
And we've seen that where we've found little pieces and we're like, "Is this yours?"
"Is this your piece?"
Yeah.
I have sometimes heard the definition of demo success for certain products, being a few pieces that comes back in, right? "You don't want to be there," I haven't heard that said.
Especially with shock. We can empty stuff out in our hands, if you go too high. We never want to induce these failures and you want to test it to its limits of course.
Once you identify that that soft failure, and usually that's enough evidence to tell you what to fix, right?
Absolutely.
You don't have to become a tiny little component example. You know if that solder joint giving you trouble, that obviously that has to be fixed. You've either got to change the solder or how it's mounted, or reinforce it, or stake it or whatever, right?
Right.
But I'm getting just as much information as that aren't things flying off the board, right?
That's correct. And many times it can if you have good monitoring techniques while you're testing. Now, what many people will do is they'll finish the testing and then say, "Okay, let's take a half a day and make it fail afterwards."
Yeah.
So take it to hard failure [crosstalk 00:31:44].
And just see what flies off or what breaks, right?
Breaks or just what quits.
Yeah. So if I can answer your question a little bit, I'd say what's too little? You're doing no testing, you're in it for the rough times. [crosstalk 00:31:56] I'm even nervous doing a new design. The whole process has been sort of illusionary that personally, I would have been hesitant to recommend [inaudible 00:32:04] new downhole design and not include it at some point.
Right.
And then too much, then you're in a gray area. This is tough. How committed I am to do this? Right. And this also becomes a little bit more tricky because unfortunately, we're not just designing stuff from a purely scientific and engineering perspective.
[inaudible 00:32:24].
There's business stuff and budgets, and how much can I spend on this? And all that kind of stuff. And so my personal opinion would be to bias as much budget as you can towards testing in your given business scenario. And then just once you get that to that point of diminishing returns, stop and go to the field.
Yeah.
So I would probably say that my personal recommendation is you be kind of on the above average to high kind of side of things for testing, versus the insane or not at all. So that's where I would be, first point.
So Ken, within the current marketplace where there's so many independent MWD companies now, if they're buying these electronics from people, is that something that they obviously should be asking? Obviously with you guys, you have that process in place.
Yeah. If I was a directional drilling company, I was buying equipment, some key questions that I would have is what's [inaudible 00:33:17] the design process of this component? And then are you doing HASS screening? If that's my job and I'm the purchasing manager or the guy picking the technology, absolutely.
And I'd be very wary of a device that wasn't already field proven, it didn't have that use in the design process. I'd suspect that once I put it downhole and put it under a lot of temperature and vibration, that there's going to be some issues that have to be worked out with that product.
Because the reality of our test world is that we see a lot of products coming in, but we see some people like you guys that are there all the time. And this is part of your culture of your company, is we want to have this as our... Moving forward, we want to make sure our testing goes to the customer.
Well, we've been converted to believers in that process, for sure. We've done the devices and seen the results. And if we felt that it hadn't given anything back to the design, we wouldn't have done it again. [crosstalk 00:34:06].
Good. So what can we expect, kind of wrapping up as the future of test and measuring. What can we do to get a little bit closer to simulating the real downhole environment? Or can we expect something else revolutionary like HALT and HASS to come out in the next 10 years?
One thing that is being talked a lot about in the HALT, HASS area is reducing a live system that does real frequency content.
Oh, okay.
And soon I think, the [inaudible 00:34:38] of the world and the manufacturers are going to possibly come up with that.
Cool.
It's not easy to do.
Was that the shock too, or just the lower frequency on top of the random?
Correct.
So you might have a table moving [crosstalk 00:34:51].
It will still be random, but you've got to have a lot more displacement of the table.
Right.
To do the low frequency.
Right.
And that's the problem.
Because look at the table right now, it's kind of like it just looks fuzzy when it's working, because it's just [crosstalk 00:35:03] And that's going to be just fantastic because if you look at kind of a frequency spectra of drilling a vibration, that's pretty much all drilling vibration energy is less than a 1,000 Hertz, right?
Way less.
Or a 1,000 cycles per second, you're capturing most of it, right?
Oh yeah. You capture it all.
And even most of it is below 500, right? And then the vast majority is still below like a 100 Hertz, right?
Right.
And so if we can get into those low one, two, five, 10, 25 Hertz frequencies, you're able to recreate a lot more of those downhole vibration runnings, right?
So just to elaborate a bit on that. The studies we've looked at, the name vibration elements in a downhole system are anywhere from one to the 50 Hertz. That's where most of them are.
And so, one Hertz of such, we're going to voom, voom, voom [crosstalk 00:35:54]
And then you get more of the shock elements that drive and stick slip, and torsional then bring you up from the 50s to the 250s.
Yeah.
But above that, there's very little that you get components of the shocks that get you [crosstalk 00:36:20]
There's an impulse of testing we made up of all [crosstalk 00:36:22].
And that's why most tests on the vibe are usually... One of the classics is I want five to 500 Hertz on the vibe table.
Even though you wouldn't have... The bit wouldn't be breaking up rocket 500 Hertz. You're going all the way up there so that you can see what happens to your chassis. You get that shock impact and then it rings at 400 Hertz.
That's right, you get the multiple.
Yeah, yeah.
So you're just covering most of the bases with that. Then you go to a 1,000 to look at the stress elements of your mechanical design.
And what's so scary about those natural harmonics, is if you find those in your design and then you just sit there and just keep hitting it, hitting it. And it's just like, it's going to come apart real quick, right?
That's right. And that's what's good about doing resonance checks under your mechanical design. So you can look at adding a few more screws here and there to tighten up your systems, things like that. That's what's good about doing vibration tests.
So sounds like what you expect is not necessarily another big revolution, but just lots of incremental improvements to the machines and the testing that we can do there?
Absolutely. Now, the other pie in the sky idea would be if somebody could come up with a 50 foot long apparatus to cover the 30 foot color, and have thermal vibration, shock pressure and bending motion, and torsional.
Okay. That sounds like a $10,000,000 [crosstalk 00:37:51].
In a controlled environment, and it may not be that far off.
Yeah.
But it's not easy.
Some rumors we're building something like that?
No, no rumors.
Yeah.
That was my pie in the sky thought, is if we can come up with something like that, I think we'd have it. But you've got to be able to control them all, [crosstalk 00:38:08] then you could really simulate downhole conditions if you had something that.
Sounds like the downhole criminal trying to build a particle accelerator or something [crosstalk 00:38:16].
Might cost as much.
And so that won't be easy to do.
Then we can simulate those downhole conditions.
Well, yeah, you're pretty darn close at that point, right? Well, Bob and Eric, thank you for joining us on today's show.
Thank you so much.
That's all the time we have for today. I'm Ken Miller.
And I'm David Erdos.
And this has been absolutely Erdos Miller New Technology podcast. You can send questions for Dave and Ken to podcast [inaudible 00:38:40] the show and we'll check out our sponsor gibsonreports@gibsonreports.com.
Erdos Miller Inc. | Copyright 2025