Completions
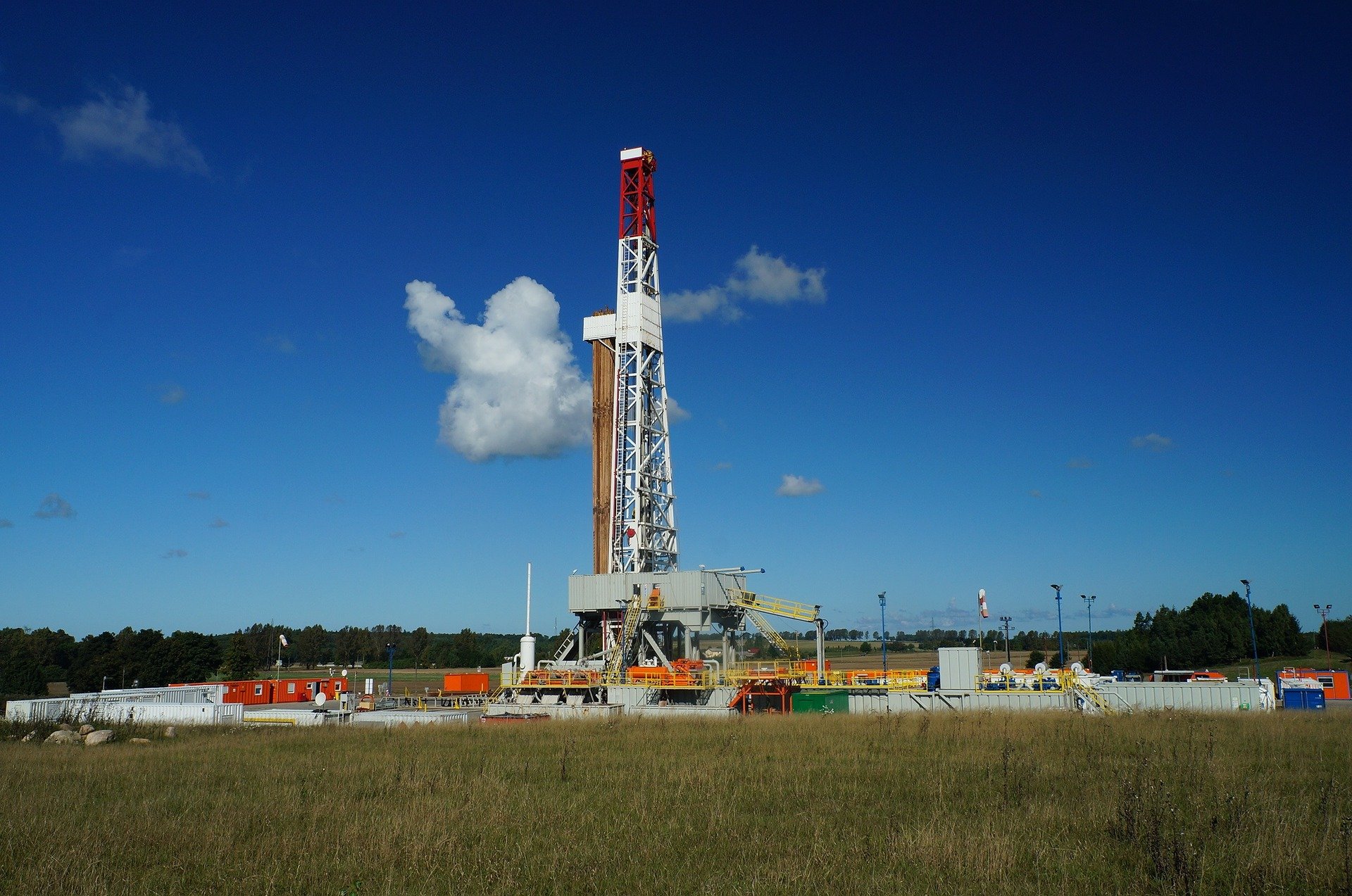
Bringing Electronics to the Completions Industry.
If you were asked 10 years ago whether electronics had any business in completions your answer would have been a resounding “no.” Today, thanks to unconventional well construction, electronics play an increasing role in cost reduction during completions. Electronic actuated systems reduce the need for wireline and slickline actuation techniques which in-turn increase ROI for the Operator.
Erdos Miller started as a down-hole electronics design house. We sharpened our skills in the drilling phase of the well construction. Although, the completions industry is a much different phase from the drilling operations, there are some overlaps in the challenges that both phases face.
In both the drilling of a well and the completions stage, any electronics that will be put down-hole must be temperature rated. It is commonplace for companies to require at least 150C rated electronics down-hole, with many jobs requiring 175C such as one of the deepest North American shale plays, the Haynesville Shale.
In addition to temperature requirements, the electronics must be ruggedized to withstand large amounts of shock. In our experience the highest shock events occur when a tool is shipped to location. However, there are cases where down-hole shock events are significant as well, such as when a tool gets stuck which requires jarring. We cannot talk about shock events without discussing vibration. Vibration is less extreme than a shock event, but constant vibration of electronics does erode the mechanical strengths of the components and boards, particularly when combined with temperature!
Aside from the temperature and shock & vibration similarities, both phases share a common problem of footprint size when discussing electronics. Whereas in drilling the tool is usually centralized, completions tools usually embed their electronics on the outside which allows for flow in the center of the tool. In either scenario, space for electronics is at a serious premium. The electronics must be thin, as short as possible, and not use tall components.
With the similarities pointed out, we must also point out the differences. One could argue that completions electronics face two additional challenges that pose serious concerns to any engineering team that will attempt to tackle them. The first and largest issue will be battery life. When drilling, the operation rarely lasts more than a week down-hole so battery life is not as important. With completions, tools may be expected to last for up to 6-months downhole. This poses a serious challenge because temperature rated batteries are incapable of storing as much energy as their room-temperature counterparts. Also, even if the electronics do not use the battery, it will slowly lose energy due to the constant heat. So even if we do nothing, the slow ticking of time will erode the battery life, this means we must be extra attentive to the components and operations we include in completions tools.
The second challenge that completions faces, is a constrained budget. As to how the completions industry was assigned the thankless job of “make it as profitable for us, while cutting costs” we don’t know. Although we don’t know the answer, we do understand that the challenge has been presented nonetheless. Constrained budget and reliable high-temperature electronics that cannot fail do NOT go hand-in-hand. The two could not be more opposite. If you want to guarantee reliability, the last thing you should do is cut costs. The best consolation we can offer, is there are some trade-offs you can make in design that will reduce cost while only slightly increasing risk. That is the real challenge at hand if all other technical problems above are solved. A method we have used in the past is to purchase non-temperature rated components and then qualify them ourselves. This allows for a cheaper component to be used in the tools that we can screen ourselves using HALT/HASS, thermal soaks and thermal cycles. Many times electronic component manufacturers de-rate their electronics to cover themselves from warranty claims. Finding these cases, are the easiest cost reductions to make that have low risk.
We enjoy the challenges presented by the completions phase of a well. If you are facing some of these alone and would rather leverage our experience, please don’t hesitate to contact us. Let us jumpstart your project so that you can focus on more world changing problems than learning how to ruggedize some electronics!
Partnerships
We believe a single company cannot take on all the challenges that MWD presents. Our method to magnifying our achievement is to create technology
partnerships with companies that are likeminded in their approach to developing cutting edge technology. Partnerships allow our MWD tool
technology roadmap to accelerate and to push forward with providing value to our customers quicker.
Partnership Opportunities
- Electronic Zonal Isolation Packer
- Smart Interval Control Valve
- Real-Time Frac Flow & Pressure System
Experience
- Smart Frac Sleeves
- Frac Fluid Mixers
- Sand Control Mixers
Relevant Downloads
Dual Telemetry Survey Report
Get a better understanding of how and where Dual Telemetry systems are being used in the industry.
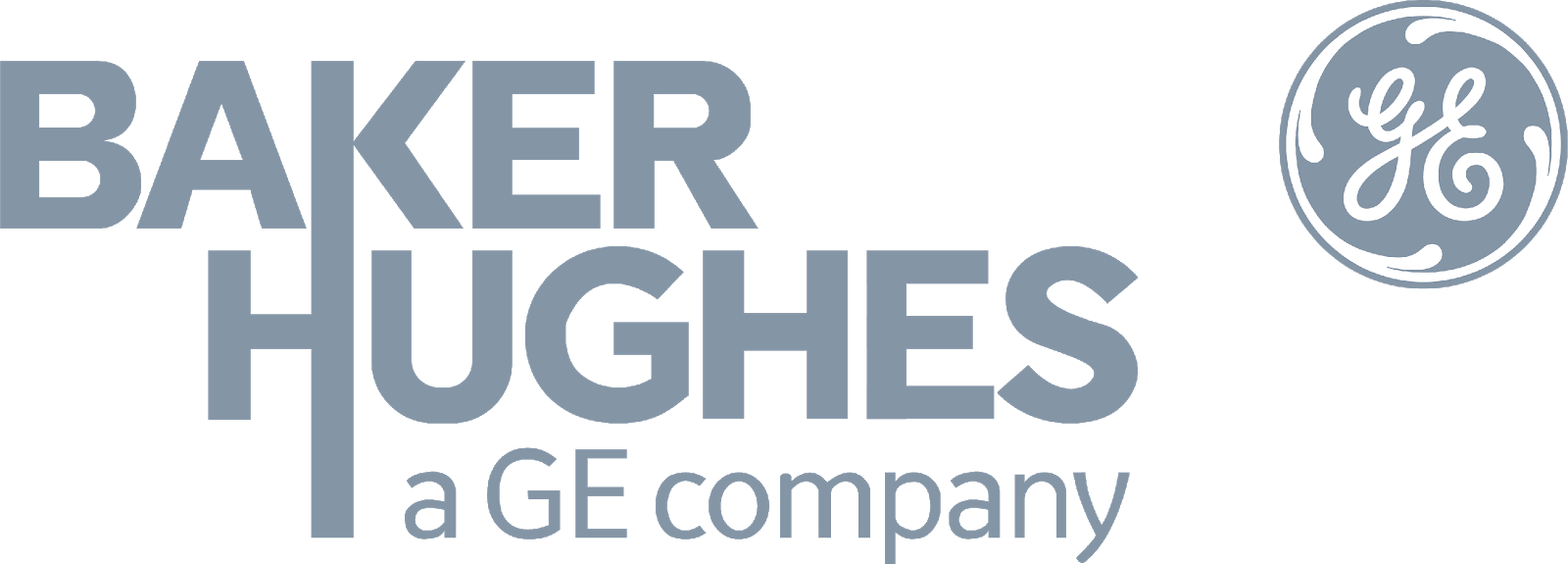



